В ОМК рассказали CNews, как цифровые технологии помогают компании в условиях дефицита кадров
Объединенная металлургическая компания (ОМК) — один из крупнейших российских производителей металлопродукции, услугами которого пользуются ведущие энергетические, транспортные и промышленные компании. В первую очередь речь идет об изделиях для добычи и транспортировки газа и нефти. Перед ОМК встала задача высвободить большое количество сотрудников для нового производства. О том, какие инновации помогли это сделать, в интервью CNews рассказала Людмила Трофимова, руководитель направления по инновационному развитию дирекции по информационным технологиям ОМК.
«Программная роботизация применима даже на производствах»
CNews: Какие виды работ вы роботизируете? Как используется программная роботизация на производстве?
Людмила Трофимова: В 2019 году мы сформулировали все идеи по роботизации, чем они выгодны для нас с экономической точки зрения, просчитали, сколько людей они позволят высвободить. Сейчас все экономически обоснованные проекты уже открыты и находятся на этапе реализации.
Мы используем роботизацию двух видов — программную и физическую.
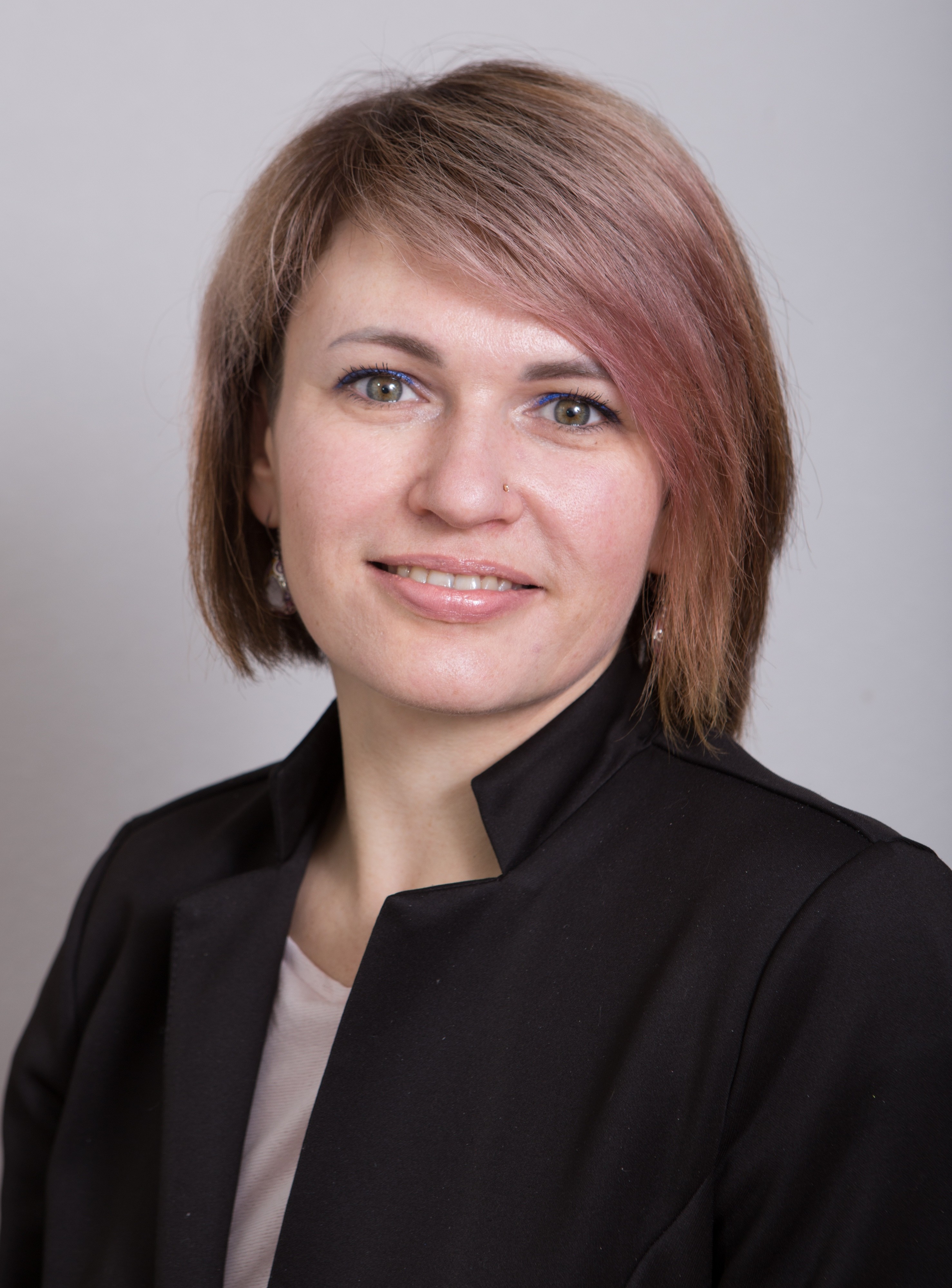
Физическая роботизация достаточно активно используется в машиностроительном, конвейерном производстве, но пока еще является дорогостоящей и редко используемой в металлургии. Мы выявили работы, которые можно передать роботам. Например, проект по автоматизированной приварке стальных планок. Пока эту работу в ручном режиме выполняют сотрудники завода. На лист стали, прежде чем начать его формовку (процесс «сворачивания» в трубу большого диаметра) четыре человека вручную приваривают четыре стальные планки. Это нужно сделать по технологии изготовления. Соответственно, если у нас две производственные линии, то восемь человек всю смену заняты приваркой планок. Это достаточно тяжелая работа, но с ней может эффективно справляться робот-манипулятор, который сам берет планку из кассеты, находит край листа, ровно прижимает к нему планку и приваривает ее. Мы выяснили, что такой робот уже успешно работает в другой металлургической компании и поняли, что такое решение для нас применимо и тоже актуально. Сейчас проект открыт, производится выбор поставщика роботов. После реализации проекта часть сотрудников останутся выполнять сервисные операции по подготовке производства и обслуживанию роботов. А около двадцати человек из нескольких смен мы сможем перевести на новые направления.
Программная роботизация экономически оправдана в большом объеме повторяющихся рутинных алгоритмизированных задач. Очевидно, что максимальный эффект от ее внедрения достигается в общих центрах обслуживания, а не в производственных подразделениях. Но оказалось, что данный инструмент здесь тоже применим. У нас, например, это формирование сертификатов качества и товаросопроводительных документов на продукцию. Сейчас совокупный эффект от реализации всех инициатив на производственных площадках с программной роботизацией оценивается в 24 штатные единицы. За год мы успели изучить несколько платформ, чтобы понять, насколько эта технология вообще нам подходит. Мы своими силами, используя пробные лицензии, которые нам предоставила компания-поставщик, за 4 месяца разработали пилотного робота, после чего убедились в том, что ожидаемый эффект будет соответствовать нашим потребностям. Потом мы продемонстрировали это решение и получили положительное решение о внедрении.
CNews: Вы упомянули, что физическая роботизация больше актуальна для машиностроения. А программная? Насколько она широко используется в России, в той же металлургии?
Людмила Трофимова: Сложно говорить про металлургию или не металлургию. Здесь правильнее будет сказать, что программная роботизация более применима пока, например, для решения финансовых задач, бухгалтерских функций, или для управления персоналом. И, по большому счету, здесь не принципиально, из какого сегмента это предприятие.
«У нас около 50 систем с компьютерным зрением»
CNews: Насколько я понимаю, вы сейчас внедряете еще и компьютерное зрение сразу несколькими проектами?
Людмила Трофимова: Тема компьютерного зрения на нашем предприятии не нова. Прямо сейчас у нас есть порядка 50 различных систем с применением этой технологии. Мы используем камеры, которые распознают маркировку продукции и номера автомобилей на контрольно-пропускных пунктах, определяют отклонения объектов в пространстве. Также у нас внедрены комплексы для измерения геометрических параметров продукции и выявления дефектов. И сейчас мы ищем места, где мы дополнительно можем ставить такие классы систем компьютерного зрения. Если говорить про измерение геометрии и выявление дефектов, то эти два сегмента присутствуют в компании, но не в очень большом объеме. Причина тому — стоимость таких установок. В частности, мы уже измеряем параметры труб большого диаметра: система в автоматическом режиме передает данные, и работает она давным-давно. Измерение геометрии — одна из важных для нас сейчас тем, однако не для всей производимой продукции находятся подходящие решения.
CNews: Что вы хотите измерять?
Людмила Трофимова: Например, геометрию колеса. В чем сложности: у колеса сложный профиль, а еще оно блестящее, практически зеркальное. И это накладывает существенные ограничения для систем компьютерного зрения. Сложная геометрия требует большого количества датчиков, а блики искажают картину и серьезно повышают требования к камерам и условиям съемки. Пропорционально сложности задачи вырастает и стоимость. Сейчас мы рассматриваем различные варианты решения этой проблемы.
CNews: А выявление дефектов — новая для вас история?
Людмила Трофимова: У нас есть несколько систем, которые по косвенным признакам помогают выявить дефекты. Но они очень специфичны и не масштабируемы на другие участки. При этом задача автоматического выявления поверхностных дефектов на продукции весьма перспективна. Сейчас визуально-измерительный контроль выполняет сотрудник: он смотрит на трубу со всех сторон и, если видит где-то изъяны, определяет их размер с помощью измерительных инструментов и принимает решение о том, нужно ли отправлять трубу на ремонт. Нам стало интересно, смогут ли системы компьютерного зрения выполнять эту работу вместо человека. Так как работающего решения именно на трубах мы найти не смогли, мы изучили схожие внедрения. У нас даже внутри компании есть решение, которое выявляет дефекты на рулонном прокате. Мы провели НИОКР, пригласили пять компаний, которые показали образцы своего оборудования и своих решений. Используются одновременно два метода: и камеры, которые дают оптическую картинку, и лазерный луч, который помогает измерять расстояние. Таким образом, накладывая две картинки друг на друга (этот метод называется «триангуляционным»), мы и видим места с дефектами, и понимаем, насколько они критичны. Сейчас ведется выбор самых оптимальных точек, на которых мы будем реализовывать первые подобные задачи.
CNews: А у вас есть какие-то ожидания от компьютерного зрения, выраженные в деньгах?
Людмила Трофимова: Мы оцениваем эффективность проекта в количестве сотрудников, которых сможем переместить на новые задачи.
CNews: Какие вообще технологии из тех, что обсуждаются сегодня, по вашему мнению, могут в ближайшие 5–10 лет оказать критическое влияние на металлургию?
Людмила Трофимова: Лично я сделала бы ставку на робототехнику, использование различных роботизированных установок, которые прекрасно дополняются искусственным интеллектом: дроны, самоходные машины. Это может существенно изменить процесс производства продукции в металлургии. Второй сегмент — это компьютерное зрение. Я считаю, что за ближайшие 5–10 лет проникновение этой технологии будет практически повсеместным. Третье направление — углубленная аналитика, которая уже сегодня помогает находить корневые причины дефектов и устранять их на ранних этапах производства, повышая уровень выхода годной продукции и снижая затраты.
«Мы не тратим время на исследования, а используем уже сработавшие где-то решения»
CNews: У вас не совсем традиционный подход к оптимизации производства. Все шаги, о которых мы говорили, вы предпринимаете в рамках концепции «умных последователей». Что это за подход?
Людмила Трофимова: Компании нужно укомплектовать новые производства в течение ближайших трех лет. Например, ОМК строит два крупных цеха металлургического завода в городе Выксе, население которого — чуть больше 50 тысяч человек. Встал вопрос: а где брать кадры для работы в этих цехах? Мало того, что ОМК нужны люди с опытом работы на металлургических предприятиях, так их еще и должно быть 3 тысячи! Вариант с привозными специалистами с учетом специфики маленького города не подходил. Конечно, это не первые проекты на заводе, ранее здесь появилось почти 5 тысяч современных рабочих мест, компания и город много чего построили для жителей из инфраструктуры, но это за предыдущие 15 лет.
В Выксе ОМК запустила проект «Тотальная оптимизация производства», задачей которого стал всеобъемлющий поиск рабочих мест на Выксунском металлургическом заводе, где можно минимизировать труд персонала, а сотрудников переводить на строящиеся производства с современным оборудованием. Как это делать? Конечно, с помощью перестроения бизнес-процессов, отказа от операций, не создающих ценность, замены ручного труда на машинный с применением цифровых технологий.
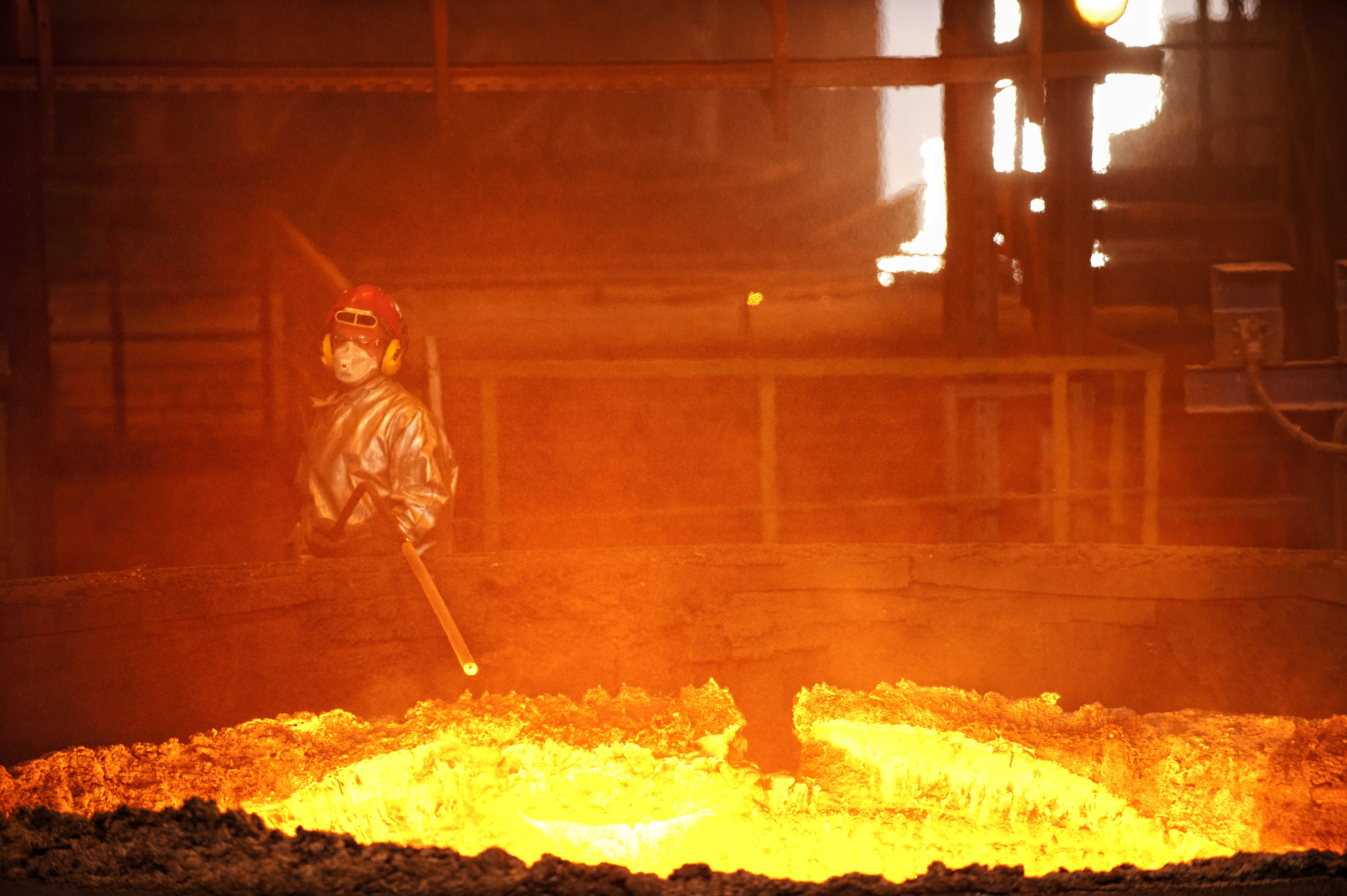
Но времени на то, чтобы выступать в роли новаторов и пробовать какие-то технологии с неясным эффектом, которые еще даже не прижились на рынке, у нас не было. Мы поняли, что с нашими задачами и сроками самое оптимальное — находиться где-то на границе «ранних последователей» и «раннего большинства», в так называемой зоне «диффузии инноваций». И поэтому точку, о которой вы говорите, мы назвали точкой «умного последователя».
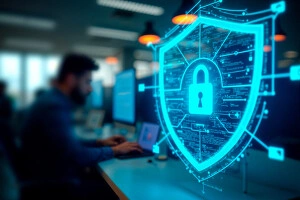
Что ОМК вкладывает в это понятие? Активный мониторинг рынка решений, постоянные коммуникации с подрядчиками и коллегами-металлургами. Цель «умного последователя» — максимально быстро обнаруживать новые работоспособные технические решения, которые мы можем использовать в ОМК. Мы не тратим время на длительные исследования в этих областях, а берем то, что уже хотя бы на одном предприятии показало результат.
CNews: А как вы отслеживаете цифровые кейсы других компаний?
Людмила Трофимова: У нас есть три типовых подхода. Самый простой вариант — читать новостные ленты различных ИТ-сообществ, ведь наши коллеги очень активно делятся своими достижениями. Найдя что-то новое для себя, мы можем выйти на контакт с компанией, пообщаться, «напроситься» в гости, пригласить их в гости к нам. Такой нетворкинг сейчас очень развит в ИТ-сообществе.
Второй вариант — участие в различных практических конференциях. Нам как «умным последователям» интересно посещать именно те, на которых компании-заказчики рассказывают об уже внедренных цифровых инструментах. Это дает возможность услышать реальное описание ситуации, возникшие при внедрении проблемы, оценить полученные выгоды, понять, на какие грабли не надо наступать и как провести внедрение более плавно и более эффективно.

И последний источник информации — наши потенциальные подрядчики. Когда они заходят с предложением своих услуг, мы в обязательном порядке просим показывать результаты реализованных проектов. А при идеальной картине — даже обеспечивать референс-визит на объект внедрения, чтобы у нас также была возможность пообщаться с представителями производств и понять, насколько данное решение нас удовлетворяет и стоит ли оно нашего внимания.
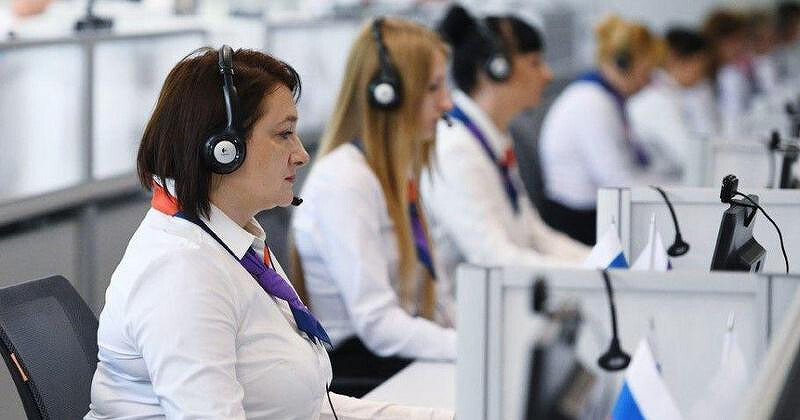
CNews: Как набиралась ИТ-команда, которая этим всем занималась? Сколько в нее входит человек и как она функционирует?
Людмила Трофимова: Внутри проекта создана экспертная группа, которая занимается анализом инициатив, связанных с цифровыми задачами и автоматизацией. В нее вошли пять экспертов из компании с большим опытом в сфере цеховой автоматики и ИТ. Группа набиралась в открытом конкурсе, на который могли подать заявку все желающие сотрудники с любых производственных площадок. Люди проходили достаточно серьезный отбор: было несколько тестов, собеседования; обязательными требованиями были знание современных цифровых технологий, наличие аналитических способностей, готовность к работе в условиях высокой нагрузки.
Эти пять человек занимаются оценкой цифровых инструментов, технологий, поиском решений, релевантных для компании и примеркой предлагаемых решений на наше производство, они же изучают экономическую целесообразность внедрения.
Понятно, что пять человек не могут обладать экспертными знаниями одновременно во всех сферах автоматизации, поэтому они активно взаимодействуют со специалистами по ИТ внутри компании, экспертами по цеховым и автоматизированным системам управления производством, системам неразрушающего контроля. На выходе мы получаем гибкую команду: пять лидеров, драйверов изменений, и большой круг сотрудников, которые дополнительно привлекаются к технической проработке и последующей реализации инициатив.